The amount of energy used by a positive displacement pump is proportional to the pump’s differential pressure. The higher the pressure added by the pump, the harder the pump is working. Reciprocating pumps accelerate the mass of fluid in the discharge line with each discharge stroke, which results in pressure spikes. A pulsation dampener reduces pressure amplitude by accumulating a percentage of fluid at discharge pressure and releasing it back into the system during the inlet stroke of the pump. With this setup, the pump only has to accelerate the fluid between the pump discharge and the dampener as the velocity of the fluid in the rest of the line remains relatively constant. Reducing discharge line pressure variation therefore reduces the total amount of energy required to support the application.
Several tests were completed using different peristaltic pumps and piping to simulate a variety of pumping conditions. The decrease in energy used over time when the pulsation dampener was added in the system ranged from 3.9% up to 34.1% depending on the setup and differential pressure created. As seen in Figure 1 below, test results using a 2.5” peristaltic pump showed a 12% reduction in energy used over time by comparing the areas under the curve for a dampened and undampened system over a 5 minute test. In all cases tested, energy savings achieved with the dampener increased with higher pump differential pressures.
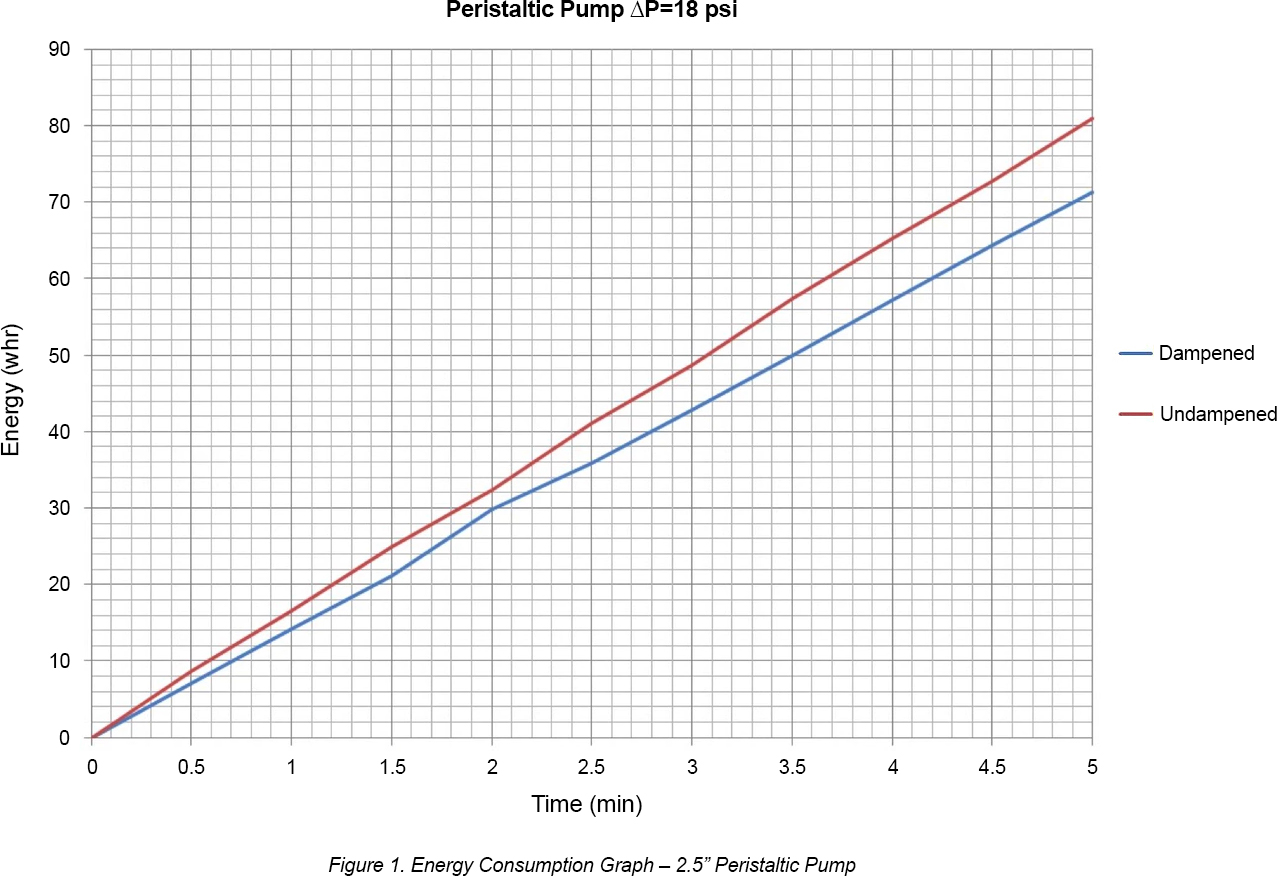
In the case of air operated double diaphragm (AODD) pumps, energy used by the pump is constant because a specific volume of compressed air at system pressure is required to fill the working chamber. However, pump flow rate in an AODD pump improves with the use of a pulsation dampener by minimizing the pressure amplitude on the discharge stroke. In other words, a pulsation dampener allows the pump to work more efficiently by limiting the fluid flow needed to repressurize the discharge line after each inlet stroke. Tests performed with AODD pumps showed increased flow rates ranging from 2.5% to 12.8% depending on differential pressure – larger differential pressures increased the flow rate observed. As seen in Figure 2 below, discharge line pressure variations reduce significantly when using a dampener, allowing the pump to operate with a nearly constant discharge pressure.
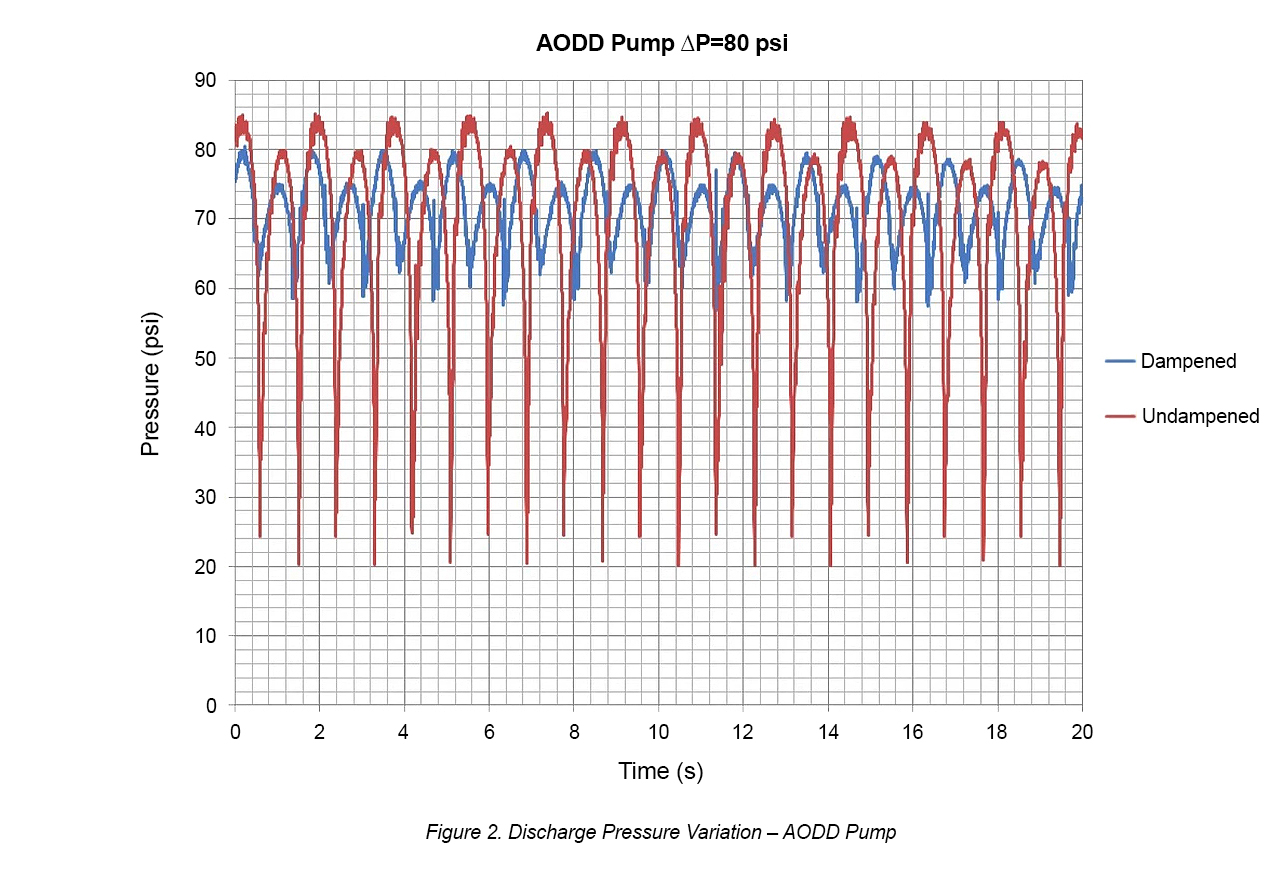
AODD pumps can save on direct energy costs by lowering system pressure but, a higher flow rate is generally more desirable. It is possible to reduce energy costs and, at the same time, increase pump flow rates by using the right dampener. Blacoh’s AODDampener™, the first pulsation dampener designed specifically for AODD pumps, features a unique fully automatic air control that automatically adjusts to keep the dampener at optimum charge. Connected to a plant’s air supply line, the automatic air control reduces dampener air consumption by using only the air needed to adjust to changes in pump discharge pressure.
Note that this energy study focused on the pump discharge pressure and how to minimize pressure variations and improve fluid flow. Additional efficiencies can be gained using inlet stabilizer dampeners to normalize inlet pressure and flow, eliminate acceleration head loss, and extend the service life of pump diaphragms and inlet system components.
The AODDampener is Blacoh’s most cost effective dampener model for systems using AODD pumps. This all stainless steel dampener is pre-sized for pumps up to 3”, features a PTFE backed diaphragm for maximum compatibility, and is offered with NPT, BSP, ANSI flange, and tri-clamp connections. Learn more at Blacoh.com/AODDampener.
Blacoh's expansive line of SENTRY™ Series pulsation dampeners, surge dampeners, and inlet stabilizer dampeners are designed for use with all types of reciprocating positive displacement pumps in a wide variety of applications across multiple industries. For more information on Blacoh’s SENTRY™ Series visit Blacoh.com/Sentry Dampeners.